Full Stack Construction
Maestro vertically integrates the design & build process through digital fabrication. We do so in a three stage process, managed via the Maestro Platform, a proprietary software tool:
- INArchitect's Design
- 01Fabrication Code
- 02Decentralised Manufacturing
- 03Digital Overlay
- OUTAsset Assembly
We start from designs of world-class architects. We don’t standardise the building product, instead delivering bespoke architecture through a digitally standardised process. The input to this process is the architect's Building Information Model (BIM).
The first step is design-for-manufacture (DfM), where we transform design intent into a set of building components. Our engineers & technical designers perform this task with the help of the Maestro Co-Pilot: a design aid that ensures that component parts are compliant with digital fabrication.
Once complete, design data is automatically transformed into manufacturing specifications: with CAD/CAM compatible instructions delivered to our production partners.
With digital instructions delivered via the Maestro Platform, our network of European manufacturers cuts, mills and forms our components using Computer-Numerically-Controlled machinery.
Partners in the Maestro network label component parts to enable downstream traceability.
Once the timber, steel, and glass components are manufactured, we pack them into the Maestro Flatpack for easy shipping by land or sea.
Each flatpack is delivered with a Digital Overlay: a web-hosted set of interactive assembly instructions. Accessing this data is as simple as scanning the QR code on any given component part.
The result? Buildings that are assembled, not constructed, cutting build times from years to weeks.
We apply our Maestro Method to mass timber and steel structures as well as the building envelope and interior partitions.
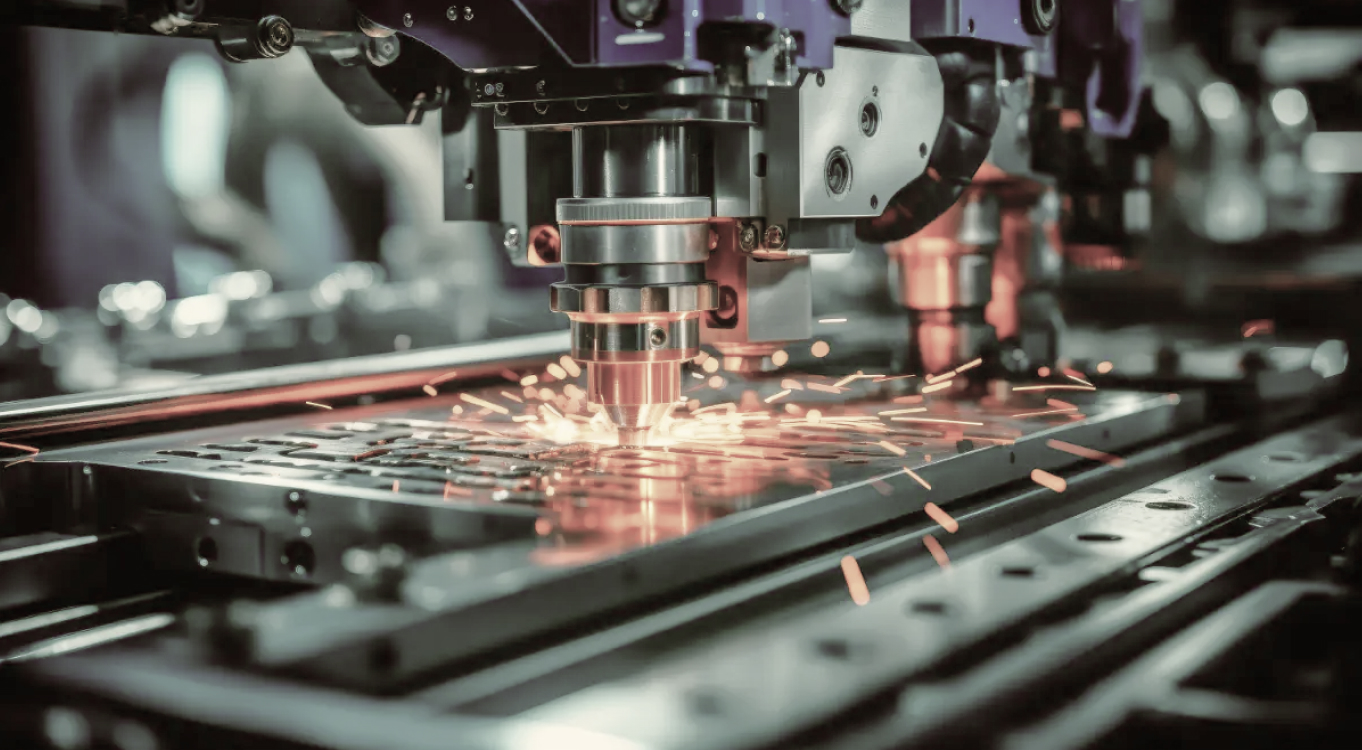
As we test the Maestro method in pilot projects across the world, the benefits are clear.
Construction simplified
We move the complexity of building from the site to the CNC machine, making the process on site simpler. No longer is your construction site a black hole of delays and cost overruns!
Build time minimised
Our component parts are designed with dry-mount assembly in mind, cutting build time. To make things even faster, our web-hosted assembly schematics enable non-specialist crews across the world to perform the assembly process.
Sustainability made real
By specializing in lightweight, shippable materials like cross-laminated timber (CLT) and light-gauge steel, we naturally reduce embodied carbon.
By simplifying construction, we lower energy usage. And by using software to track the entire process, we automatically calculate every gram of our carbon footprint. This allows us shorten supply chains, minimize resource use, and maximize building lifespan to make the most of resources used.